Pattern Making Methods in the Garment Industry
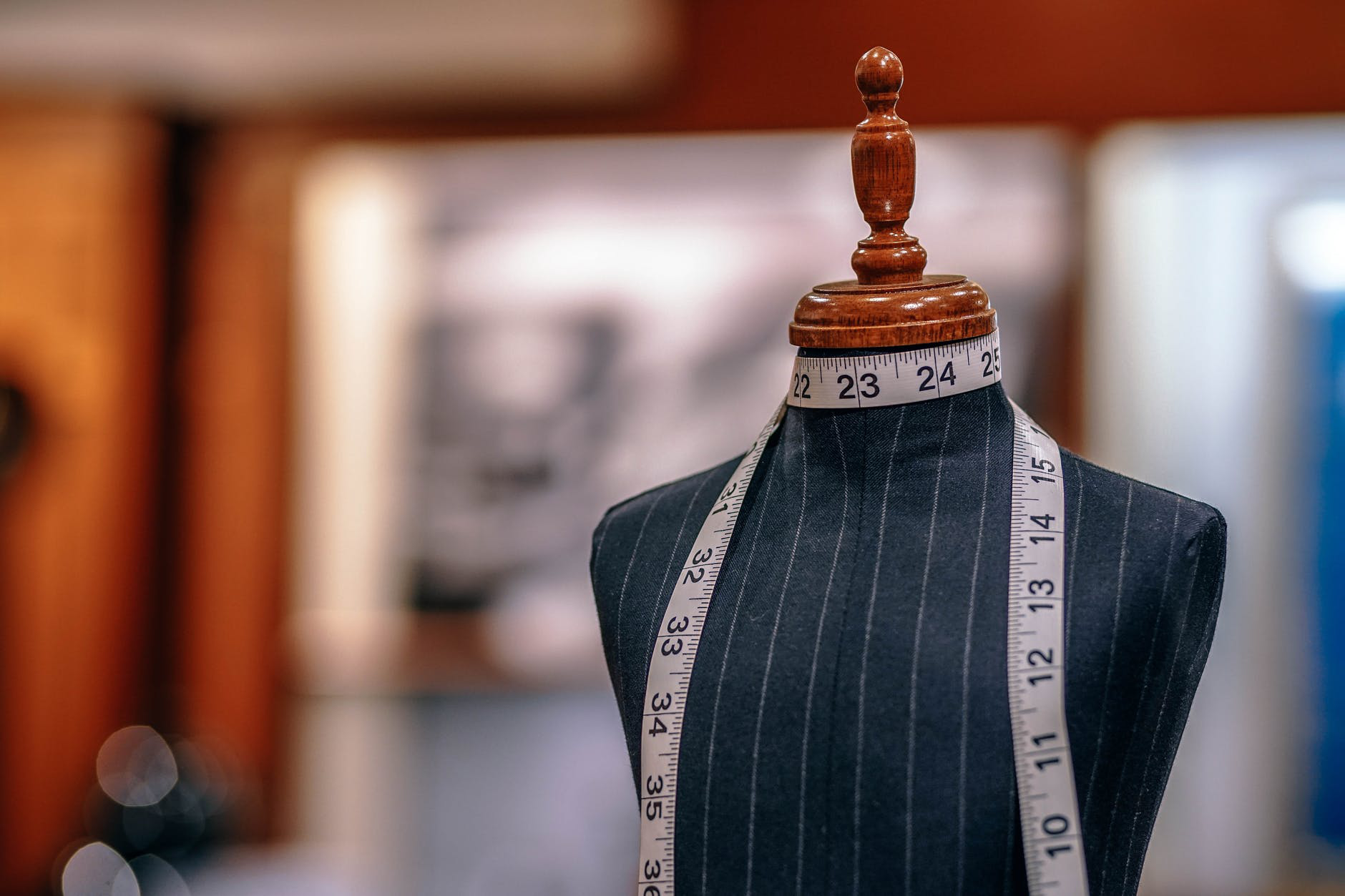
No design can ever be successfully translated from the imagined “oohs and aahs” to the realized steps of walking “wowzas” without pattern making; it is one of the most fundamental steps of a dress production process.
Basically, pattern making is the skill of producing a two-dimensional design representation of a garment using specific tools, measurement charts and tailoring techniques.
Think of it as creating a design blueprint for apparel before putting the design to implementation and fabricating an inspired new garment out of it.
How do designers go about pattern making?
Well, it depends on what pattern making method has been chosen for a given dress design process.
There are mainly two types of pattern making methods:
· Drafting
· Draping
Let’s take a quick look at them one by one.
Drafting
Drafting is carried out on a piece of brown paper or on an advanced computer program, where initially the designer takes measurements of the wearer for whom the dress is to be designed. Once the measurements have been taken, a basic pattern is drawn for each piece of the garment on the paper on screen. This drawing can be done manually or using a CAD software. The resulting pattern carries information such as the location of grain lines, sizing, cut numbers etc.
In the final step, the individual patterns (forming a pattern set) are pinned onto the fabric, and any required modifications are made. The fabric pieces are then cut, assembled and sewn together to give shape to the apparel product.
Drafting ensures a design with an extremely accurate fit and is the most used pattern making method by fashion designers.
Draping
Draping is the older of the two pattern-making methods. And while it isn’t as popular as it once used to be, it still remains a key skill among premium design houses.
Unlike drafting, draping works by directly positioning and pinning the fabric on a mannequin. The fabric pieces are then manipulated to develop the structure of the garment design. These fabric pieces are usually of muslin; however, in some cases, draping is also done using calico or the final fabric itself.
Fashion designers drape a garment in sections, i.e., front skirt, back skirt, front bodice, back bodice etc.
Once the desired design is achieved, the draped fabric is marked to indicate essential design information. It is then removed from the dress form and processed for truing.
In the final steps, excess fabric material is cut away and the trued fabric is placed back onto the mannequin to check for fit accuracy. The design is now ready to be transferred to paper and for sewing.
Are you an aspiring fashion designer planning to launch your own label?
Lefty Production Co. can help you.
We’re a leading Los Angeles garment manufacturers and clothing manufacturing companies in Los Angeles. Our clientele includes both small and large brands. Reach out to us for more information.